Just to pass the time away, of course. Anyway, I reserve the right to use Engineer in Progress to ruminate on ideas I like, and last night I saw a really interesting one. Ray MacVay, from
Blue Max Studios (makers of the hard-scifi RPG
Tales of the Black Desert), made an interesting post entitled
Artificial Gravity and What Rollercoasters Can Teach Us, and it solidly engaged what someone of my acquittance once called my "turbonerd" mode. The proposal is to use self-propelled train-like cars moving around a fixed circular rail for large spin-gravity spacecraft, instead of a large rotating structure. I'm not really explaining it well, and he does a much better job, so...go read
the original post. I'll wait.
 |
Seriously, go check it out. It has pictures. |
Done? All right, let's talk the engineering of such a system. First of all, I like a lot about it. Air doesn't need to cross the spin division because entire cars do, presumably each with on-board life support, water reprocessing, and that stuff. Power and data are a bit trickier--unless the cars have their own on-board power generation, then electrical power will still have to be sent to the cars with slip rings, and data will have to be sent from car to car either with a wireless network or (if wired is preferred) another slip ring setup. Still, it's an interesting modular system. Still, there's one or two things that need work.
First is that I'm not sure about having the spin rails out on pylons from the sides as they are above. They're going to be fairly beefy, and then they have to also support the modules going around the track. Why is this an issue? Time for a structures lesson. Imagine a ship under thrust, consisting of an engine, a support truss (A&B) and two spin rings on pylons (C&D). Essentially, this is a simplified version of Ray's IPV design.
 |
Might look something like this |
Under thrust, the structural loads on A and B will be compressive, that it that the forces are along the axis of the beam, trying to push it to make it shorter. This isn't bad--metals' not half bad at compressive, it's why the use of steel was key to early skyscrapers. However, on C and D, the load is perpendicular to the axis of the beam, so instead of being a compressive load, it's a shear load. If you imaging the metal as being sort of flexible, you could imagine it bending like a spoon being used as an improvised catapult. Metal really does bend like that under shear loads (though not as dramatically as that spoon), and if you're going to be running rails on those beams, that's an issue. Thus, the first change I'd suggest would be to move the spin rings to being axial, like this:

In this configuration, the majority of the forces are now compressive, and the only shear-loaded members are the actual spin rail supports, which are shorter and can be more numerous, reducing the stress on any individual beam.
The other thing that bugged me about the concept was the sidetrack concept Ray introduces. On the one hand, it's nice since it allows people to move from the spin sections to the stationary sections (including radiation-shielded shelters for solar storms) without leaving their modules, which is very nice and worth having--it's an innovative thing, and one reason I like the concept. On the other hand, it means more complexity, and this requires consideration. First, since the rail section needs to keep it's center of mass placed properly, every car must be balanced by the other cars (two cars 180 degrees apart, 3 cars at 120 degrees, 4 at 90, ect....), and it makes sense to have the ability to take off or add two cars at a time from opposite sides to be able to maintain this balance. So instead of just one switch in the spin rail, you need two 180 degrees apart.
These switches will also need to be quick-cycling. If you have several cars going around your spin rail and you want to take off only one of them (or two, for balance), then you need to be able to cycle the switch to get the car off and cycle it back to the straight position before the next car comes through. To get an idea of just how fast they need to cycle, you need to know how fast the cars are moving and the number of cars on the rails. By my analysis of his drawings (like the one above), the life modules are about 4 m in diameter, and the spin ring track is about 28 m in diameter, for a spin radius of 18 m. Using
SpinCalc, this gives the following figures for 1 G:
 |
Run with Ray's size and 1g generated |
So, this requires an angular velocity of 7 RPM, which is a bit too high. Re-running with a lower spin velocity (5 RPM, about the highest I'm comfortable assuming people can adapt to) and the same size parameters gives the following:
 |
Run with Ray's size and 5 RPM |
This gives only about half Earth gravity, which is possibly enough, though long-time readers may remember me lamenting that lack of real data on how much gravity is needed to avoid long-term issues. SpinCalc can also be used to see what spin radius would be needed for 1 g and 5 RPM:
 |
Size required for 1 g with 5 RPM |
As you can see, the spin radius has to be 35.77 m, which with the 4 m modules is a rail diameter of almost 70 m. This is...a lot. Going from 0.5 g at 5 RPM to 1 g at 5 RPM requires bumping the diameter up by basically a factor of 2. That's a pretty significant change and I think you can see why I believe good data on long-term human health at gravity levels between 1 g and microgravity is necessary if spaceflight is really going to be practical. Anyway, what does this mean for the switching speeds needed?
At 7 RPM, it takes about 8.57 seconds for a car to go around the track. With 4 cars on the track, the time between cars is only 1/4 that time, or 2.14 seconds. This is the margin that the switches have to cycle within. Even at only 5 RPM, the window with 4 cars on the rails is only 3 seconds-still very short. Can a switch be made for this? Maybe, but it's going to be tricky.
Anyway, moving on from the question of how the switches need to operate to how rails would need to be run. The track layout Ray shows on
his example here basically can be though of as translating to the following diagram.
 |
Diagram of Ray's basic tracks |
The two spin rails are connected to one sidetrack each. As I said, there really need to be two switches on each spin rail so that modules can be kept balanced. This results in the following modified track diagram:
 |
Modified Track Diagram |
Here, I've added a second set of switches to each spin rail, and also a through track connecting the two side tracks. The connection allows a car to be easily moved from one sidetrack to the other, or for cars to be re-arranged with the switches. The switches are a bit more complex than the switches in the original version, but the system should be much more useful.
I also looked at possible track arrangements for axially-located spin rail like I suggested at the start. The best I came up with was the below. Note that the system is modular--it works for one, two, three, or more spin rings.
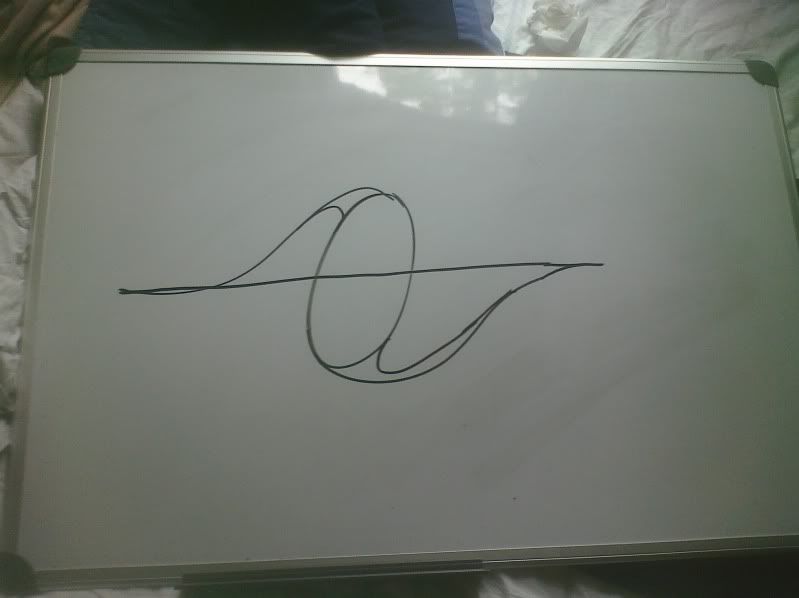 |
Track diagram for axial spin rail |
Anyway, so that's basically everything I've got at the moment. To close, here's some pictures of something cool I saw when I was dropping by the Aerodesign wind tunnel on Friday. I was walking along, and I suddenly noticed that the cart that a guy was pushing out of the machine shop had something pretty nifty. They were metal cubes, but they were kind of different.
So, I stopped for a closer look. The cubes were 1 ft cubes of aluminum honeycomb, lots of little cells connected together. Apparently they were being prepared for some experiments involving flight data recorder crash survival, as targets. We've used honeycomb material in Aero team a little, but never metal, and never this thick (our would be more like a sheet, with the cells only about 0.125 to 0.25 inches deep). Anyway, it was nifty stuff, and I'm glad the guy was willing to stop and let me have a look.
Apologies if the scale looked ambiguous; the minimum diameter I would consider for this kind of set up is 50 meters, with ten meter diameter modules. I would prefer 100 meter diameter spin rails, so that the RPMs are low enough to allow switching on and off the spin rail without having to slow the other modules down.
ReplyDeleteI also agree about putting the spin rails on the primary axis. I was enamored of the side track design and wanted to exploit that. However, it's looking like more trouble than its worth. A side track between two counter moving spin rails that allows damaged modules to be removed for repair may be for feasible.
ReplyDelete